Thanks to the well-developed technology of FlowVision; the basics of a classical CFD project workflow is changing...
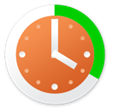
While developing and improving FlowVision; our main intention is allowing simulation engineers to focus on the physics of the case which is the essential objective of their work. On the other hand, classical CFD approaches and workflows leave engineers with no choice but make a great effort for geometry manipulations, meshing and similar tasks which are not the end but means of an engineering analysis process.
Traditional CFD
|
FlowVision
|
|
Geometry and Meshing
- Import Geometry
- De-Feature
- Prepare for Meshing
- Mesh Generation
- Original CAD geometry is lost and only mesh elements remain depending on resolution
|
|
Geometry and Meshing
- Import Geometry
- Automatic Mesh Generation
- Original geometry is maintained without any simplifications.
|
|
|
|
|
|
|
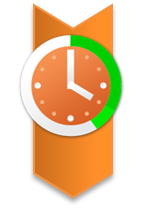 |
Specification of Model
- Assign boundary conditions on mesh elements.
- Specifying project parameters
|
|
Specification of Model
- Assign boundary conditions on surfaces of actual CAD geometry.
|
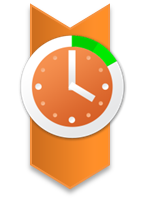 |
|
|
|
|
|
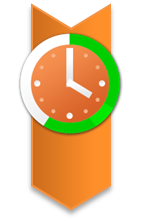 |
Simulation and Post-Process
- Usually you can use or MPI or Threads parallelization
- Visualization of Results only after Simulation is Totally Completed
|
|
Simulation and Post-Process
- You can use hybrid parallelization: MPI with Threads
- Visualization of Results after 1st Iteration (Real-Time Post Processing during Simulation)
|
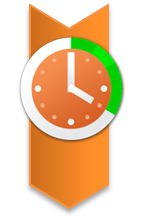 |
|
|
|
|
|
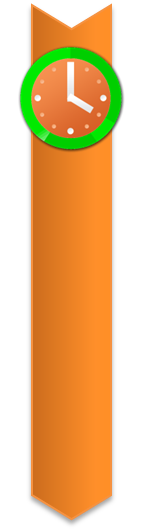 |
Shape Optimization
- Import New Geometry (De-Feature and Prepare for Meshing)
- Re-Mesh
- Repeat Model Specification
- Restart Simulation
|
|
Shape Optimization
- Replace Geometry (Since BC’s are connected to geometry, not to mesh, geometry and/or mesh can be changed quickly without re-building whole project.)
- Restart Simulation
|
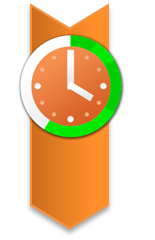 |